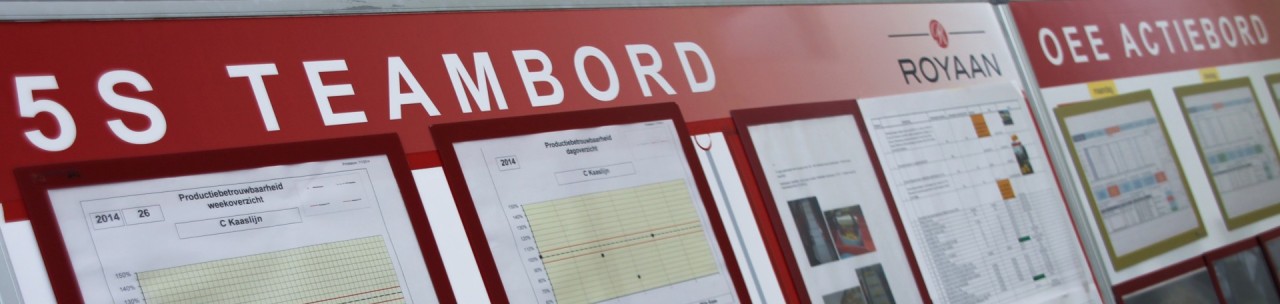
“We willen dat onze medewerkers zich betrokken voelen”
‘Uw verwenner in warme snacks’ is de slogan van Royaan, producent van diepvriessnacks voor onder andere MacDonalds. De bedrijfsnaam zal niet iedereen bekend in de oren klinken, maar Royaan is wel verantwoordelijk voor klinkende namen zoals de Van Dobben- en de Kwekkeboom-kroket. Het bedrijf produceert op vijf locaties in Nederland, onder andere in Wijk bij Duurstede, waar ook het hoofdkantoor gevestigd is. Daar is Frans Binnenhei sinds 2009 manager van de productieafdelingen. De laatste jaren is Royaan goed op weg met het ‘lean’ inrichten van de verschillende productieomgevingen.
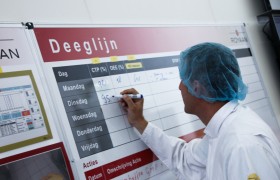
Meer verantwoordelijkheidsgevoel
“De cultuur binnen Royaan is informeel en no-nonsense. We spreken elkaar direct aan als er iets is”, vertelt Binnenhei. “Maar wat we daarnaast graag willen is dat onze medewerkers verantwoordelijkheidsgevoel hebben en zich op de werkvloer ondernemender gedragen. Om dat te bereiken, zijn we begonnen om inzichtelijk te maken wat dat precies betekent; dat een verbeterproces niet alleen maar een plan is dat het management achter gesloten deuren bedacht heeft. Voor iedereen in dit bedrijf moet het een dagelijkse bezigheid worden. Daarom zijn we, bij wijze van kick-off, aan de slag gegaan met 5S (scheiden, schikken, schoonmaken, standaardiseren en stand houden). Sindsdien zijn we ook steeds meer lean-middelen gaan ontwikkelen en gebruiken, waarbij Visual Workplace ons voorziet van de juiste kennis en producten op het visuele vlak.”
De aandacht erbij houden
In de aanloop naar 5S maakte Royaan een inventarisatie van wat er allemaal beter kon op het gebied van orde en netheid binnen het bedrijf. “Er stonden vieze schoenen en wasmanden die overstroomden van het vuile wasgoed, om maar wat te noemen. Maar ook apparatuur waarvan niemand wist waarvoor die diende”, herinnert Frans zich. “We hebben alles gefotografeerd. Die beelden zijn voor iedereen duidelijk: daar moet wat aan gebeuren. Maar na verloop van tijd merk je dat de aandacht weer verslapt als mensen niet regelmatig met dit soort dingen geconfronteerd worden. Daarom hebben we besloten de vorderingen op een groot bord te registreren, in plaats van in mappen. Dat bord hebben we in de gang opgehangen, zodat iedereen het kan zien, ook de uitzendkrachten die hier in groten getale rondlopen. Het gevolg is dat mensen er schik in krijgen om de resultaten die op het bord te zien zijn te verbeteren.”
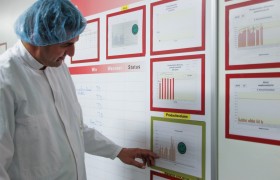
Samenwerking met Visual Workplace
Voor het ontwikkelen van die borden nam Binnenhei contact op met Visual Workplace. “Visual Workplace heeft mij erg goed geholpen met het ontwikkelen van de borden. Ik was in eerste instantie op zoek naar stickers om zelf een bord mee te maken, maar toen vond ik Visual Workplace. Zij konden mij borden leveren die helemaal aangepast waren aan de wensen van Royaan, compleet met ons eigen logo. Op internet had ik een paar voorbeelden gezien van 5S- en OEE-borden, maar die waren allemaal erg standaard. Ik heb mijn ideeën aan Visual Workplace voorgelegd en aan de hand daarvan hebben zij een ontwerp gemaakt. Door de snelle communicatie over en weer zijn we vlot tot een goed bord gekomen dat we nu veelvuldig gebruiken.”
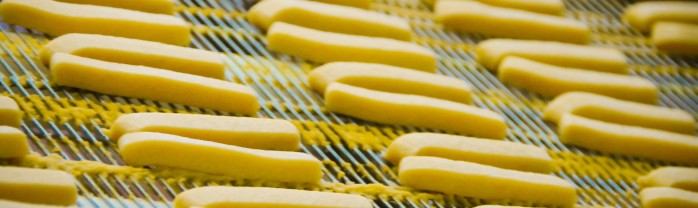
Lean verder uitrollen
Voor Frans Binnenhei is lean manufacturing een persoonlijke passie geworden. Hij raakte geïnspireerd door de praktijkvoorbeelden die hij tijdens zijn reizen door Japan tegenkwam bij bedrijven als Subaru. “In een productiebedrijf als dit moeten we constant bezig zijn met verbeteren, niet alleen omdat regelgeving en moderne productiemethodes dat van ons verlangen, maar ook omdat we daar winst uit kunnen halen voor het bedrijf”, legt hij uit. “Daarom zijn we na de succesvolle introductie van 5S meteen doorgegaan met het verder uitrollen van lean. We hebben werkgroepjes in het leven geroepen die per periode tien verbeteringen aan moeten dragen.”
Het succes van SMED
Eén van die werkgroepen ging aan de slag met SMED (single minute exchange dies), een lean-methode om ombouwtijdenvoor productielijnen te verkorten. Dat werd een enorm succes. Was de ombouwtijd voor de inpaklijn eerst nog 45 minuten, nu is die teruggebracht naar 10 minuten of minder. “Voordat we begonnen met dit proces heb ik een filmpje gemaakt van het ombouwen. Dat heb ik daarna nog een keer gedaan. Die twee filmpjes spreken boekdelen. En het mooie is dat de verbeteringen door de betrokken medewerkers zelf aangedragen zijn”, aldus Binnenhei.
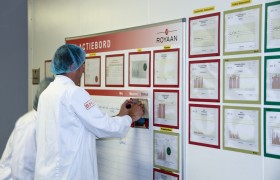
Visualiseren
Om het proces gaande te houden, is visualisatie noodzakelijk. “De borden van Visual Workplace gebruiken we onder andere om in het ochtendoverleg terug te halen wat er de dag daarvoor gebeurd is, bijvoorbeeld op het gebied van storingen en kwaliteitsissues. Eerst deden we dat aan tafel, nu staand in de gang bij het bord. Dat doen we met opzet. Zo houden we de vaart erin en medewerkers die langslopen vanuit de kleedkamers kunnen dan zien dat er echt iets gebeurt met de problemen die zij gemeld hebben. Verder hangen er in de gangen overal borden waarop we laten zien wat er allemaal gebeurt in de fabriek. Iedereen mag die borden gebruiken.”
Eigenaarschap
Binnen Royaan heeft lean een vaste plaats gekregen. “Er is al veel bereikt,” zegt Frans Binnenhei, “maar we zijn er nog lang niet. Sommige verbeteringen leveren direct tijd en geld op, andere zijn moeilijker meetbaar. Het belangrijkste is, dat medewerkers zich eigenaar voelen van hun stukje van het productieproces en daar ook de verantwoordelijkheid voor nemen.”
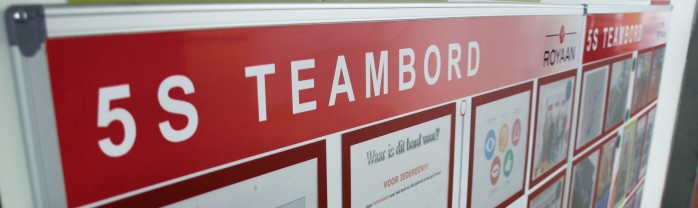