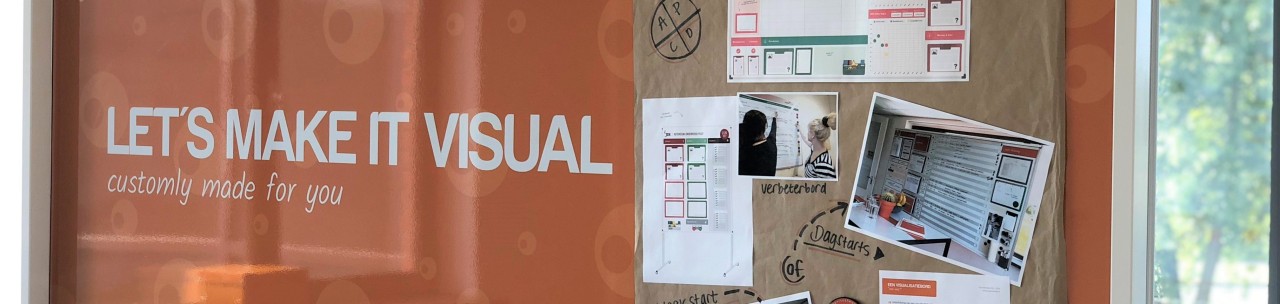
Diversen Lean verbeter tools | visual management borden
Hieronder vindt u een korte omschrijving van de overige lean methodes. Voor elke methode hebben wij een toepassing lees hieronder meer of neem contact op met een van onze werknemers en laat u adviseren.
Dagelijk Ochtend Overleg (DOO)
Het dagelijks ochtendoverleg. Het dagelijks ochtendoverleg kent 3 doelstellingen:
- Performance review
- Escalatie en afhandelen van afwijkingen
- Continu verbeteren
Performance review
Tijdens het dagelijks ochtendoverleg komen op een vast tijdstip vertegenwoordigers van een proces verantwoording afleggen over de KPI’s (Key Performance Indicatoren). Dit gebeurt vaak d.m.v. een visualisatiebord.
Escalatie en afhandelen van afwijkingen
In het dagelijks ochtendoverleg worden alle afwijkingen behandeld van een proces die niet opgelost kunnen worden door de vertegenwoordigers. Door op een gestructureerde manier ondersteuning te vragen van een ondersteunende afdeling is voor een ieder in de organisatie duidelijk wat de status en het actieplan is van een issue.
Continu verbeteren
Een resultante van deze review en escalatieproces zal inzicht geven in het verborgen verbeterpotentieel. Multidisciplinaire aanpak met een gestructureerde probleem oplossingsmethode aanpak (PDCS, DMAIC) zal leiden tot continu verbetering van de processen.
Het dagelijks ochtendoverleg moet ondersteund worden middels excellente visualisatie. Visual Workplace kan u als partner hierin helpen. Neem contact met ons op voor meer informatie.
Kai-Zen (Kaizen methode)
Kaizen is japans voor "veranderen naar beter" of "verbetering" en is een aanpak in productiviteitsverbetering. Het Toyota Production System is vrij bekend om zijn kaizen. Bij Toyota wordt van medewerkers verwacht dat zij, in geval van afwijkingen, eigenhandig de productielijn gestopt wordt. Om vervolgens samen met collega's en supervisors te werken aan verbetering. De cyclus van Kaizen methode kan gedefinieerd worden als:
- Standaardiseer een activiteit
- Meet vervolgens de standaard activiteit (cycle time/ inventory)
- Controleer de meetmethodiek op juistheid
- Verbeter de activiteit
- Standaardiseer de nieuwe manier van werken
- Start de volgende Kaizen cyclus
Een beter definitie van het Japanse gebruik van de Kaizen methode is "uiteen halen en opnieuw in elkaar steken op een betere manier." Datgene wat uiteen gehaald wordt is meestal een proces, een systeem, een product of een dienst. Kaizen is een dagelijkse activiteit met een doel dat verder gaat dan verbetering. Het is ook een proces dat, wanneer correct uitgevoerd, de werkplaats menselijker maakt: het elimineert hard werk (zowel mentaal als fysiek) en het leert mensen de verspillingen in een proces zien en elimineren.
Opex (Operational Excellence methode)
Het begrip operational excellence komt voort uit het boek “The disciplines of market leaders” geschreven door Treacy en Wiersema. Daarin worden 3 pijlers beschreven voor een goed draaiende onderneming: Customer Intimacy, Product leadership en Operational Excellence. Hierbij is Operational excellence het realiseren van een onderscheidende marktpositie door het leveren van producten en/of diensten met uitmuntende operationele prestaties die tot uiting komen in zaken als lage prijs, betrouwbare levering en goede service. Operational excellence focust zich op het reduceren van de operationele kosten.
Een beter definitie van het Japanse gebruik van de Kaizen methode is "uiteen halen en opnieuw in elkaar steken op een betere manier." Datgene wat uiteen gehaald wordt is meestal een proces, een systeem, een product of een dienst. Kaizen is een dagelijkse activiteit met een doel dat verder gaat dan verbetering. Het is ook een proces dat, wanneer correct uitgevoerd, de werkplaats menselijker maakt: het elimineert hard werk (zowel mentaal als fysiek) en het leert mensen de verspillingen in een proces zien en elimineren.
Six Sigma
Six Sigma is gebaseerd op statistisch denken en kent zijn oorsprong in de kwaliteitscirkel van Deming (PDCA, Plan-Do-Check-Act). Daarnaast wordt er een vaste methodologie gebruikt om problemen op te lossen, namelijk de DMAIC methode. DMAIC is een afkorting voor (Define Measure Analyze Improve Control). DMAIC is generiek toepasbaar in elk bedrijfsproces. Six Sigma heeft een uitgekristalliseerde infrastructuur met task forces. Six Sigma wordt door velen gezien als een vervolg op bestaande management methodieken, waarbij vaak wordt uitgegaan van Statistische Procesbeheersing (SPC) als onderliggende aanpak.
DMAIC en Six Sigma visualisatieborden
Het visualiseren van een Six Sigma proces is een belangrijke stap in het werk van de Six Sigma teams. Door visualisatie zijn zowel de deelnemers van de Six Sigma processen als de medewerkers betrokken bij de verbeterprocessen. Visualisatie kan geschieden door middel van een DMAIC bord (Define Measure Analyze Improve Control). Een voorbeeld van een DMAIC bord is te zien op een afbeelding rechts. Op de DMAIC borden wordt de informatie uit de diverse stappen gepresenteerd door middel van magneetvensters of magnetische ringbanden.
RCA (Root Cause Analysis)
In een Root Cause Analysis wordt een fout of probleem stapsgewijs geanalyseerd, om terug te gaan tot de grondoorzaken waardoor het veroorzaakt is. Mbv een oorzaak-gevolg diagram worden de oorzaken in kaart gebracht. Pas als een goed beeld is gevormd van de grondoorzaken, kunnen acties afgesproken worden om de grondoorzaken aan te pakken. Deze acties voorkomen dan vergelijkbare problemen in de toekomst.
Visualisatie is een krachtig hulpmiddel om tot de route cause te komen. Visual Workplace ondersteund veel klanten in hun probleem oplossingsstructuur. Dit kan zijn met behulp van verbeterborden, PDCA/DMAIC borden maar ook door visualisatieborden met een visgraatdiagram (Fishbone) te leveren of A3 problem solving kaarten/visualisatieborden.
Naar de grondoorzaak: 5 times why. Een techniek om een grondoorzaak te vinden is “5 times why”. Bij een gevolg vraag je waardoor het veroorzaakt is. De oorzaak die je vind is een gevolg van iets, dus vraag je wederom waardoor dat veroorzaakt is. Na zo’n 5 keer doorvragen kom je bij de grondoorzaken. Dit zijn de oorzaken die je aan kunt pakken, om soortgelijke problemen te voorkomen.
Deze grondoorzaken hebben vaak meerdere problemen tot gevolg, en daardoor is het aanpakken van de grondoorzaken meestal zeer lonend.
LOTO
Visualisatie speelt een belangrijke rol in het totaalproces van een LOTO strategie. Van het visualiseren van de basisstappen, het visualiseren van de LOTO sloten, het LOTO bord en natuurlijk de LOTO procedure in beeld.
Waarom LOTO?
Ontoereikende procedures voor de besturing van gevaarlijke energieën vormen de belangrijkste reden voor ongevallen. Een typisch geval doet zich voor wanneer medewerkers de machine opnieuw starten en zij zich er niet van bewust zijn dat er nog onderhoudswerkzaamheden worden verricht. Ongevallen vinden ook plaats omdat zich nog altijd potentiële energie in de machine bevindt nadat deze van de energiebron is gescheiden. Een effectieve mogelijkheid voor het veiligheidsmanagement met betrekking tot de besturing van energie is de toepassing van een geschikte Lock Out Tag Out-procedure (herinschakelblokkering/markering, LOTO).
Wat is LOTO? LOTO staat voor Lock out Tag out
Het doel van LOTO is het vergroten persoonlijke veiligheid bij uitvoeren van werkzaamheden! Tevens dient het ervoor te zorgen dat er geen gevaar/risico voor anderen of de machine ontstaat. Dit gebeurd door het (zelf) energievrij maken en houden van machines/apparaten (door hangen sloten - sleutel in eigen beheer) “Energie”-vormen zijn: stoom, elektra, perslucht, veerkracht, laser-licht, oliedruk, zwaartekracht, temperatuur, product of grondstof aan-/afvoer.
Wanneer gebruiken we LOTO:
- Indien (rest) energie gevaar oplevert voor jezelf, anderen of machine.
- Indien sprake is van verhoogd risico (met meerdere personen aan dezelfde machine werken).
- Bij twijfel.
- Technisch ingrijpen. Wijzigen van het ontwerp, waarbij gereedschap wordt gebruikt, onderdelen worden losgenomen. Standaard veiligheidsvoorzieningen voldoen niet meer. LoTo is verplicht.
- Indien gevolg zéér ernstig is.
Altijd bij werkzaamheden aan apparatuur waarbij, in geval van een incident, het gevolg zeer ernstig kan zijn. Visualisatie speelt een belangrijke rol in het totaalproces van een LOTO strategie. Van het visualiseren van de basisstappen, het visualiseren van de LOTO sloten, het LOTO bord en natuurlijk de LOTO procedure in beeld.